Mining Element at Mining World Russia 2023
The latest equipment and machinery show for the mining industry (MWR 2023) turned out to be the largest exhibition in years. Despite the departure of many major manufacturers, all three Crocus Expo pavilions were filled. New players, new tasks, and projects were brought to the stage. We’d like to tell you why Mining World Russia 2023 was memorable for us and sum up the results in a quick report.
A trend toward efficiency and smart operation
This year, the interest of customers in wear-resistant materials and conveyor components exceeded the expectations of Mining Element and Nordfelt. At Mining World Russia, our team brought a bunker lined with all types of wear-resistant plates. This exhibit has already starred in more than one exhibition. After all, it allows us to clearly demonstrate the benefits of a combined lining, providing protection against several types of wear at once.
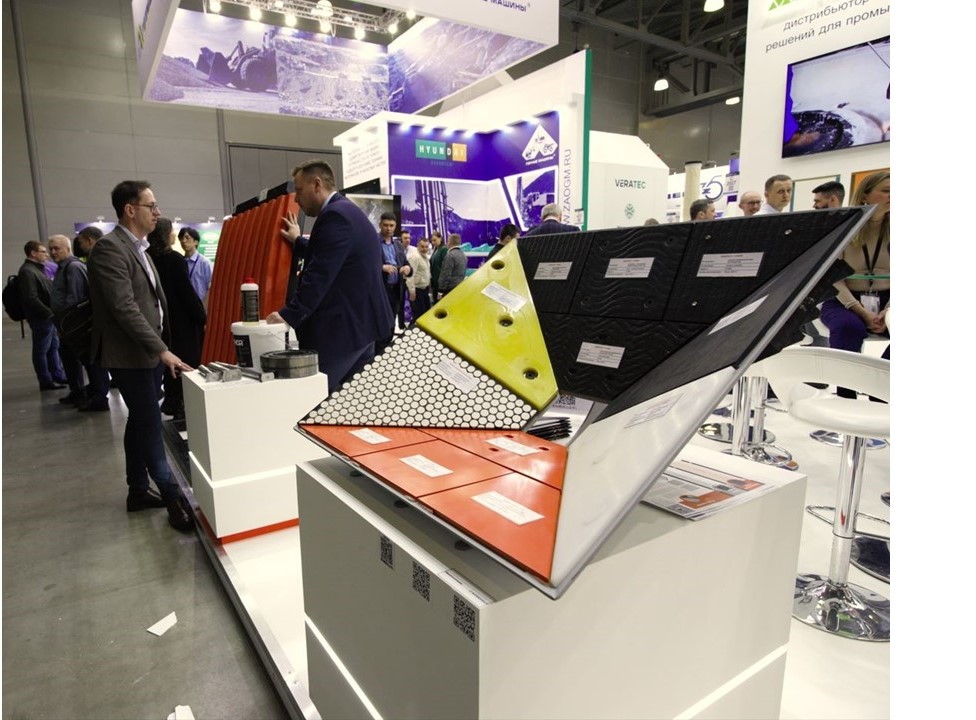
Also, Mining Element presented a new solution: a lining with magnets, which reduces the time for replacing plates by ten times.
“Today, the main trend in the market is that the equipment that was installed at enterprises in the 80-90s has been subjected to great physical wear. Foreign equipment that was brought to Russia in the 2000s is also outdated, and enterprises are looking for solutions to modernize it. Many GOKs are now engaged in technical re-dressing of equipment,” commented Olga Stepuk, Head of Wear-Resistant Solutions at Mining Element.
Stand attendees also received many questions about conveyor components. These products allow you to maintain the original throughput of the conveyor for a long time and reduce the loss of transported material. Considering that only a few companies supply special conveyors to Russia now, enterprises are interested in extending their service lives.
Reverse engineering and equipment modernization
In the context of a shortage of supplies for OEM equipment, along with the process of updating equipment, enterprises are looking to retain existing assets. This is confirmed by a large number of requests for the production of components by reverse engineering. Increasingly, customers turn to Mining Element with requests to produce spare parts according to their drawings. Alternatively, they look to scan and develop design documentation for parts for specific equipment installed at the enterprise. Often, when implementing such projects, Element’s specialists manage not only to reproduce the parts but also to introduce new solutions that increase the efficiency of the machines.
By the way, at the exhibition, customers were interested not only in the issue of replacing OEM components but also in meeting the demand for spare parts for Russian, Chinese, and Turkish equipment, which was installed at mining and processing plants this year.
“We see more and more requests for import substitution of spare parts for original European equipment. Now, orders have begun to appear for the production of components for Russian, Chinese, and Turkish equipment. If you look at the geographical distribution of expo attendees, you can see that there are much more suppliers of equipment from these countries than in previous years,” said Ivan Shunyakov, Head of the Department of Crushing and Sorting of Ore Materials at Mining Element.
Unique accessories
There were requests at the exhibition that cannot be called an obvious trend, but they are also largely related to import substitution. For example, the modernization of spare parts for slurry pumps. Such solutions allow one to increase the efficiency of the equipment and reduce the costs of the enterprise.
“Sometimes customers need to increase the life of spare parts at critical nodes, for example, at mill unloading sites,” explained Alexey Kostrikov, Director of the Mining Element Hydrotransport Department, “This approach allows us to reduce the costs of the enterprise that arise, for example, due to the fact that the schedule for the maintenance work of the equipment involved in joint processes does not match. The increase in the life of wear parts helps to combine the operating time of devices so as not to stop production several times for relining. Sometimes, for these purposes, you need to use a different alloy for the part, sometimes you need to change the geometry or even choose a spare part with different characteristics.”
Mining Element and Nordfelt specialists also noted an increase in the demand for spare parts for rare or exclusive types of equipment. Previously, OEMs sold a large volume of parts for such machines, which was enough for enterprises for 1-2 years. Therefore, even when European companies announced that they would stop working in Russia, the extractive factories were not very worried, thinking that their stocks would be enough until the OEMs set up supplies. A year later, it became clear that Western brands weren’t returning for the time being, and now, GOKs are looking for suppliers who can offer quality alternatives for rare equipment.
“The market has changed a lot this year. Given that Western manufacturers have stopped working in Russia, there is a great need for the quality replacement of OEM products. Mining Element receives a lot of requests for reverse engineering. Enterprises need to compensate for the damage caused by the cessation of supplies of equipment and spare parts of Western brands,” commented Marat Abdurahimov, Development Director of Mining Element. “Our company has also changed this year. We have mastered the production of new product lines, and our range has greatly increased. Therefore, during this time, we have become market leaders in providing spare parts for mining equipment.”
We use cookies to enhance your browsing experience, analyze site traffic and serve tailored advertisements. By continuing to browse or closing this banner, you consent to our use of cookies. Read more about how we use cookies.Cookie Policy