News
Mining Element Optimizes Equipment Performance for Greater Efficiency
Ivan Shunyakov, Head of the Crushing and Ore Sorting Department, presented a report at TECH MINING Siberia 2025 (March 12-14) on modernizing the crushing process to improve operational efficiency. His presentation highlighted key challenges and priorities that mining companies face today.
see moreCelebrating Eight Years!
Supporting mining companies in optimizing their production processes has always been the core mission of Mining Element. On January 24th, the company marked its eighth anniversary by reaching out to customers to learn about their experiences with Element spare parts.
see more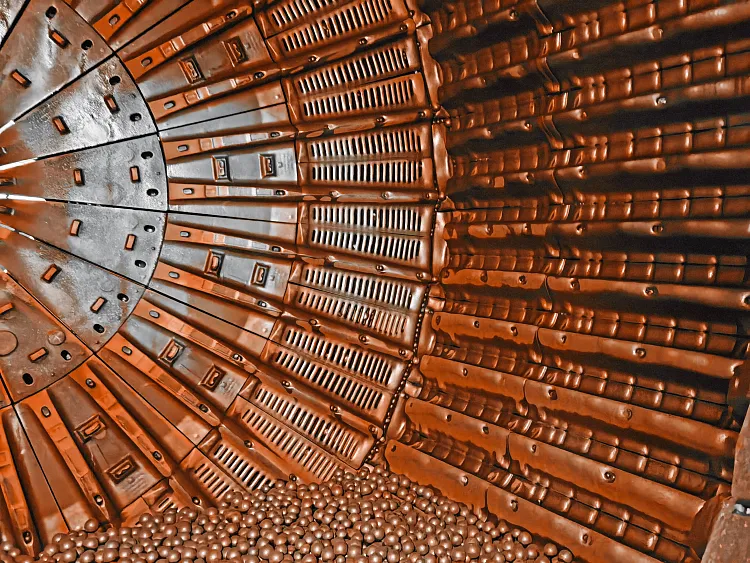
Mining Element Sells its Mill Lining Product Portfolio
On January 1, 2025, ROITECH acquired Mining Element’s mill lining business. The portfolio includes rubber, rubber-metal, metal, and magnetic liners, along with discharge grates.
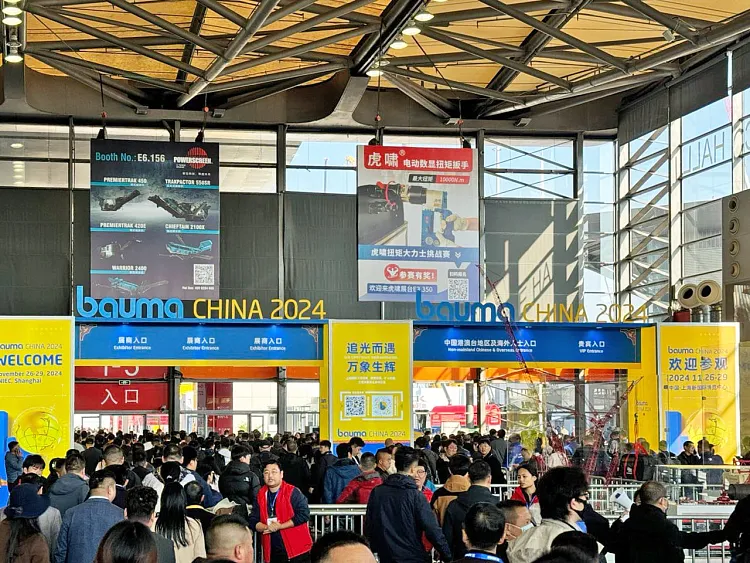
Mining Element is in Demand in China
The international construction and mining equipment exhibition, Bauma CHINA 2024, has come to a close in Shanghai. It brought together representatives from manufacturing industries across China, as well as Turkey, Italy, and Germany. The specialists from "Mining Element" in both the Chinese and Russian offices held productive negotiations at the Element stand.
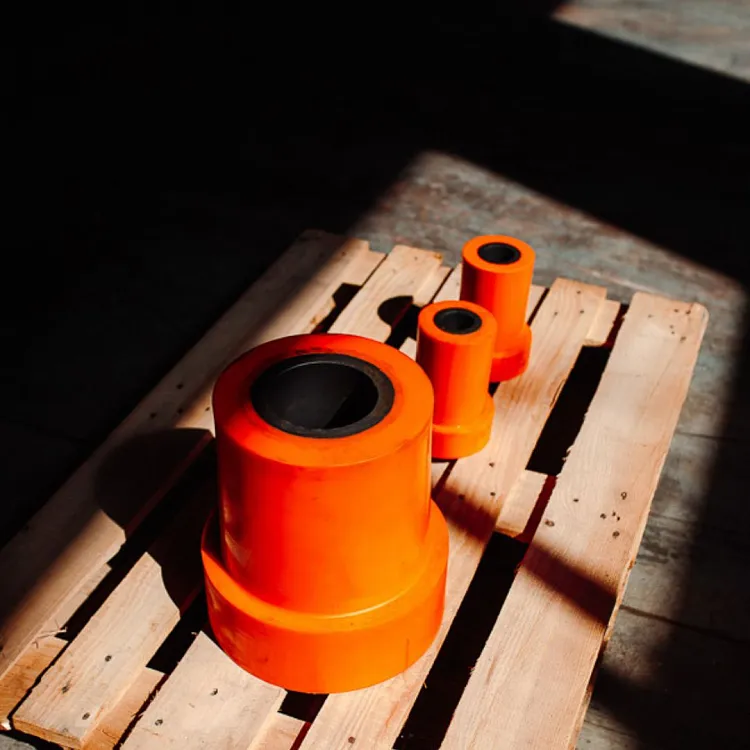
Far East Gold Processing Plant Tests Element Sand Nozzles
A major gold mining company in the Russian Far East conducted pilot industrial tests (PIT) of Element sand nozzles for the CAVEX 500 hydrocyclone.
Murmansk Regional Mining Complex Unveils New Projects
The 13th International Mining Conference, Barents-Arctic Economic Partnership (BAEP-2024), held in Kirovsk, focused on advancing key enterprises in the region and tackling the critical workforce shortage in the industry.
see more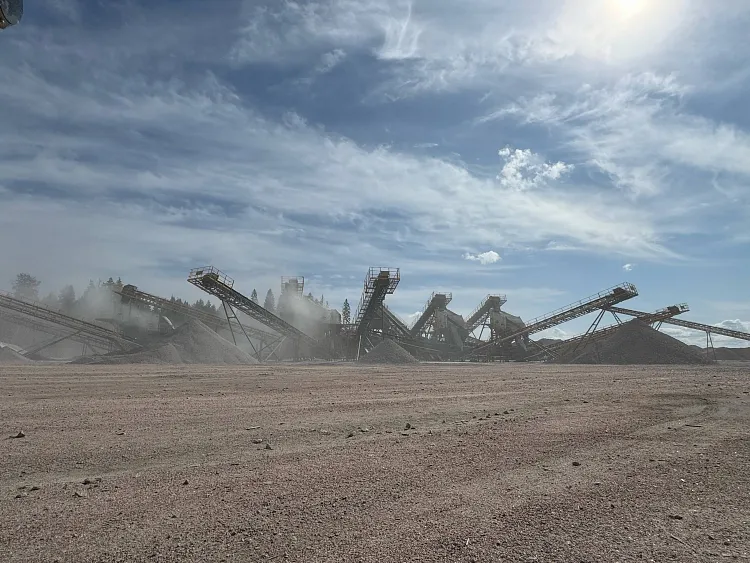
Video Report: Mining Element Visits a Quarry in Karelia
This summer, specialists from Mining Element and their official dealer Northern Standard visited the Karelprirodresurs site near the village of Elisenvaara. The goal was to scan newly installed quarry equipment and discuss plans for future collaboration.
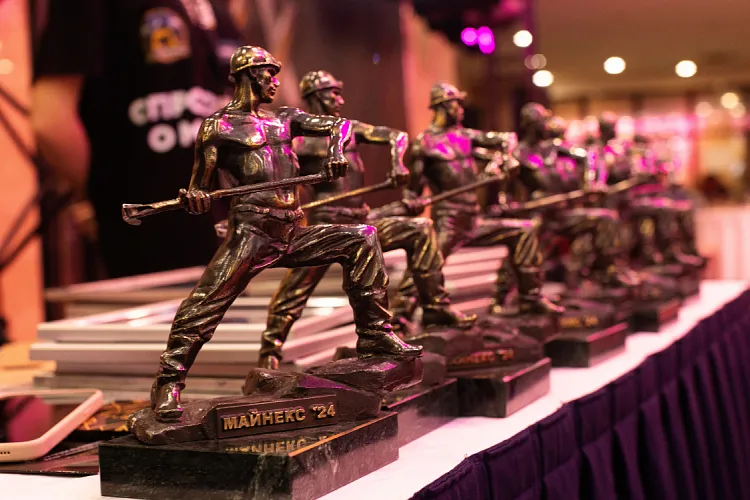
Mining Element Seeks Collaboration for Localized Production
Specialists from Mining Element’s underground drilling division participated in the "MINEX Russia: People and Technology" conference, offering key observations on the state of the industry. They emphasized the urgent need for collaboration among domestic drilling equipment manufacturers to prevent rising production costs.
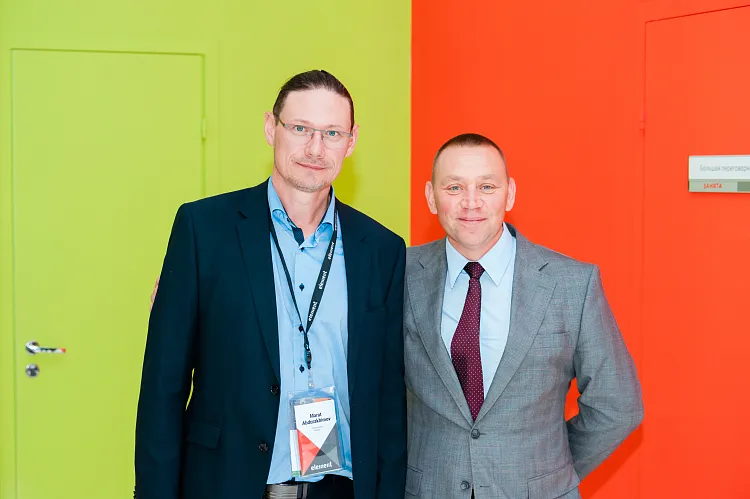
Nordfelt JSC is now an official distributor for Mining Element, a manufacturer of spare and wear parts, in a partnership status change.
Nordfelt has proven itself to be a reliable partner. The effective collaboration between both organizations has demonstrated that they are ready to expand their cooperation. As the official distributor, Nordfelt now holds the status of exclusive representative for the manufacturer, responsible for driving sales growth and development.
We use cookies to enhance your browsing experience, analyze site traffic and serve tailored advertisements. By continuing to browse or closing this banner, you consent to our use of cookies. Read more about how we use cookies.Cookie Policy